Product information "TMS Taper Manufacturing Station"
Manufacturing of Optical Fiber Tapers, Couplers, Combiners; “Ring of Fire” Heat Source for Even Heating; Integrated Cleaver for ≤500 µm Dia. Fibers; Flow 126 l/min; Pressure 0.4-0.6 Pa
3SAE Technologies’ TMS Taper Manufacturing System with an integrated cleaver is the supplier’s most advanced optical fiber tapering system that provides easy fiber access, unparalleled heating source control, stiction-free pulling results in the highest quality, lowest loss and best repeatability.
The production-ready TMS system is specifically designed to maintain production-level repeatability for manufacturing of optical fiber tapers, couplers and multi-kilowatt class high-power fiber combiners.
The TMS operates in partial vacuum (advantageous in producing adiabatic fiber tapers) and is utilizing the patent pending “Thermally Stabilized Plasma™” technology, which generates a wide and extremely stabilized heat source with a wide dynamic range of operation from <300 to >3000 °C. This allows the width of the plasma field to expand up to 10x along the axis of the fiber.
While narrow profiles create modulations and stress concentrations that induce losses, heat sources with a wider heat profile are better for tapering and bundling of fibers because the pull distance per unit time is distributed over the molten region in accordance with the profile. The TMS system’s wider plasma field flattens and reduces the frequency of modulations in a taper, resulting in ultra-low losses <1%.
Operating in partial vacuum also minimizes oxidation of the electrodes during the tapering process, resulting in virtually debris free tapers. 3SAE Technologies’ blunt electrode design increases life expectancy by >10x while increasing throughput power capabilities for high-power laser systems. High-power testing confirms that TMS does not contaminate the glass surface, eliminating the need for etching and reducing the cost of production and rework.
Three customizable tapering modes are available: single direction, bi-directional and table-based tapering. Table-based tapering allows the flexibility of a syntax-based software program to create a custom taper program while using a simplified LabVIEW-based GUI. Alternately, programs such as "MATLAB" or Microsoft Excel can be utilized to develop the tapering program.
Key Features:
- Unsurpassed Heat Source Circumferential Thermal Uniformity for Symmetrical Ultra-low Loss Tapering and Reduced Thermally-induced Component Stress
- Contamination-free Heat Source Capable of Producing Ultra-high Strength and Multi-kilowatt Class Optical Fiber Tapers and Combiners
- Fastest Cycle Times Based on Standard Splice, Taper and Cleave Cycle Times Averaged Together
- In-situ Cleaver Included for Fiber Diameters ≤500 µm
- Patent Pending “Thermally Stabilized Plasma™” in Partial Vacuum, Resulting in Highest Quality, Lowest Loss and Best Repeatability
- Three Customizable Tapering Modes: Single Direction, Bi-directional and Table-based Tapering
- Ultra-low Contamination for High-power Applications
- Blunt Electrode Design Increases Life Expectancy by >10x
- Dimensions: 75 x 31 x 28 cm, Weight: 44 kg
- Power Supply: 24 VDC, 200W
- TMS Ships With PC System With Windows Operating System, Serial Communication to TMS Mother Board and a 23” 1920x1080 High-resolution Wide Screen Monitor
- Flow: 126 l/min
- Pressure: 0.4 to 0.6 MPa (~60 to 90 psi)
Applications: Manufacturing of Optical Fiber Tapers, Couplers and Multi-kilowatt Class High-power Fiber Combiners; Maintaining Production-level Repeatability
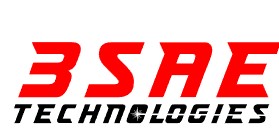