Product information "SHOTMASTER SX Desktop Dispensing Robots"
Control System Electronic; Number of Axes Controlled 3, 4; Travel Range 50-500 mm; Operating Speed 1-800 mm/s; Repetitive Position Accuracy ±0.01 mm, ±0.01°
Mushashi Engineering’s SHOTMASTER SX series of high-speed desktop dispensing robots provides a fusion of “core” dispensing technologies and 3-axis motion units. With a maximum speed of 800 mm/s, the SX series offers top-level operation speed in desktop class.
Available with X- and Y-axis working areas from 100 to 500 mm, these dispensing robots are suitable for a variety of workspace environments. In addition to this series’ ±0.01 mm accuracy, Musashi Engineering’s patented “Synchro Speed™” function maintains a constant line width even when moving through a corner, resulting in a maximum reduction of cycle time for the highest production efficiency.
Musashi Engineering’s SHOTMASTER SX series allows fully automated, fast and high-precision 3-axial dispensing – for example dispensing various optical adhesives in photonics applications.
A broad portfolio of accessories is available for Musashi Engineering’s dispensers, ranging from high-precision, high-quality, highly reliable syringes & accessories to unique nozzles and needles that can handle any type of fluid and dispensing requirements as well as other accessories for dispensers.
Specifications:
Item Name | SHOTmini100Sx | SHOTmini 200Sx | SHOTMASTER 300Sx | SHOTMASTER 400Sx | SHOTMASTER 500Sx | ||||||
Model | SM100SX3A-SS | SM200SX3A-SS | SM200SX3A-Z-SS | SM200SX4A-SS | SM300SX3A-SS | SM300SX4A-SS | SM400SX3A-SS | SM400SX4A-SS | SM500SX3A-SS | SM500SX4A-SS | |
Number of Controlled Axes | 3 Axes | 4 Axes | 3 Axes | 4 Axes | 3 Axes | 4 Axes | 3 Axes | 4 Axes | |||
Travel Ranges | X, Y-Axes | 100 mm | 200 mm | 300 mm | 400 mm | 500 mm | |||||
Z-Axis | 50 mm | 80 mm | |||||||||
W-Axis | − | − | − | ±360° | − | ±360° | − | ±360° | − | ±360° | |
Setting Range of PTP Operation Speed (*1) | X, Y Axes | 1 to 800 mm/s | |||||||||
Z-Axis | 1 to 350 mm/s | 1 to 250 mm/s | 1 to 400 mm/s | ||||||||
W-Axis | − | − | − | 1 to 900°/s | − | 1 to 900°/s | − | 1 to 900°/s | − | 1 to 900°/s | |
Setting Range of Interpolation Operation Speed (*1) | X, Y Axes | 0.1 to 800 mm/s | |||||||||
Z-Axis | 0.1 to 350 mm/s | 0.1 to 250 mm/s | 0.1 to 400 mm/s | ||||||||
W-Axis | − | − | − | 0.1 to 900°/s | − | 0.1 to 900°/s | − | 0.1 to 900°/s | − | 0.1 to 900°/s | |
Repetitive Positioning Accuracy (*2) | X, Y Axes | ±0.01 mm | |||||||||
Z-Axis | ±0.01mm | ||||||||||
W-Axis | − | − | − | ±0.01° | − | ±0.01° | − | ±0.01° | − | ±0.01° | |
Transportable Weight (*3) | Y-Axis | 8 kg | 15 kg | ||||||||
Z-Axis | 2 kg | 3.5 kg | 2.5 kg | 7 kg | 6 kg | 7 kg | 6 kg | 7 kg | 6 kg | ||
Rated Power Supply | 100 to 240VAC, 50/60 Hz | ||||||||||
Power Consumption | 100 W | 120 W | 200 W | 220 W | 200 W | 220 W | 200 W | 220 W | |||
External Dimensions (*4) (Excluding Protrusions) | Width | 202 mm | 300 mm | 510 mm | 610 mm | 710 mm | |||||
Depth | 290 mm | 300 mm | 570 mm | 670 mm | 770 mm | ||||||
Height | 440 mm | 455 mm | 555 mm | 590 mm | 690 mm | 590 mm | 690 mm | 590 mm | 690mm | ||
Weight | 11 kg | 13.3 kg | 14.5 kg | 15.5 kg | 37 kg | 40 kg | 55 kg | 58 kg | 66 kg | 69 kg |
*1 These values vary depending on the operations, the weight and gravity center of the loaded object, or other factors.
*2 This value is measured by the method prescribed by Musashi Engineering (measuring method in conformity with JIS).
*3 When options are not mounted. The value varies with setting speed, setting acceleration/deceleration time, and operations.
*4 Width and Depth are the dimensions of the lower section of the case.
Key Features:
- Ultimate Cost-effective Performance
- High Speed: 800 mm/s
- Accuracy: ±0.01 mm
- Control Method For Each Specified Axis to Move to the End Coordinates: PTP Control (at Each Speed), Interpolation Control (at the Total Interpolated Speed)
- Interpolation: 3-D Line, 3-D Circular Arc/Circle, 3-D Elliptic Arc/Circle, Spline
- Number of Input/Output Signal Points: 26 General-purpose Input Points, 26 General-purpose Output Points
- Program Entry Method: Teaching Pendant, PC
- New Type Teaching Pendant Equipped With Interactive, User-friendly Interface, Stopwatch and Dispensing Condition Switching Function as well as Data Transfer Function Between Robots
- Program Capacity: 40,000 Steps (999 Channels)
- Program Storage System: Internal Memory, Back-up on PC With Dispensing Pattern Editing Software
- Program Editing Software: MuCAD V (Optional)
- Options: Hight Extension, Nozzle Adjuster, Purge Cup, Additional Axis, Other
- CE Marking Certified, EU RoHS Compliant
Applications: Fully Automated, Fast and High-precision Dispensing of Optical Adhesives, Solder, UV Adhesives, Threadlockers and Other Fluids
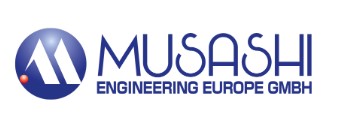