Product information "SHOTMASTER OmegaX Desktop Dispensing Robots"
Control System Electronic; Number of Axes Controlled 3; Travel Range 80-500 mm; Operating Speed 1-500 mm/s; Repetitive Position Accuracy ±0.005 mm
Mushashi Engineering’s SHOTMASTER OmegaX series of high-precision and high-rigidity desktop dispensing robots provides a fusion of “core” dispensing technologies and 3-axis motion units. With its repetitive positioning accuracy of ±0.005 mm, the SHOTMASTER OmegaX series offers high levels of dispensing quality for enhanced yield.
This series’ high rigidity allows high-speed, stable operation of heavy-duty tools and work pieces. Equipped with Musashi Engineering’s patented “Synchro Speed™” function, SHOTMASTER OmegaX dispensing robots achieve a constant drawing width regardless of robot speed, reducing cycle time to a minimum for ultimate production efficiency.
Available with X- and Y-axis working areas from 200 to 500 mm, these dispensing robots are suitable for a variety of workspace environments. Musashi Engineering’s SHOTMASTER OmegaX series allows fully automated, high-precision and high-rigidity 3-axial dispensing – for example dispensing various optical adhesives in photonics applications.
Improved linkage with the dispenser enables reconfigurable dispense conditions from robots, simple test shot for improved dispensing quality, 3D/spline interpolation and simple, automatic correction of the nozzle position after syringe replacement.
A broad portfolio of accessories is available for Musashi Engineering’s dispensers, ranging from high-precision, high-quality, highly reliable syringes & accessories to unique nozzles and needles that can handle any type of fluid and dispensing requirements as well as other accessories for dispensers.
Specifications:
Item Name | SHOTmini 200 OMEGAx | SHOTMASTER 300 OMEGAx | SHOTMASTER 400 OMEGAx | SHOTMASTER 500 OMEGAx | ||||||
Model | SM200OMEGAX-3A-SS | SM300OMEGAX-3A-SS | SM400OMEGAX-3A-SS | SM500OMEGAX-3A-SS | ||||||
Number of Controlled Axes | 3 Axes | |||||||||
Control Method (*1) | PTP Control, Interpolation Control | |||||||||
Travel Range | X, Y-Axes | 200 mm | 300 mm | 400 mm | 500 mm | |||||
Z-Axis | 80 mm | |||||||||
PTP Operation Speed Setting Range (*2) | X, Y Axes | 1 to 500 mm/s | ||||||||
Z-Axis | 1 to 400 mm/s | |||||||||
Interpolation Operation Speed Setting Range (*2) | X, Y Axes | 0.1 to 500 mm/s | ||||||||
Z-Axis | 0.1 to 400 mm/s | |||||||||
Interpolation | 3D Line, 3D Circular Arc / Circular, 3D Elliptical Arc / Ellipse, Spline | |||||||||
Repetitive Positioning Accuracy (*3) | X, Y Axes | ±0.005 mm | ||||||||
Z-Axis | ±0.005mm | |||||||||
Transportable Weight (*4) | Y-Axis | 20 kg | ||||||||
Z-Axis | 15 kg | |||||||||
Rated Power Supply | 100 to 240VAC, 50/60 Hz | |||||||||
Power Consumption | 130 W | 180 W | ||||||||
External Dimensions (*5) | Width | 380 mm | 510 mm | 610 mm | 710 mm | |||||
Depth | 460 mm | 570 mm | 670 mm | 770 mm | ||||||
Height | 590 mm | 590 mm | 590 mm | 590 mm | ||||||
Weight | 30 kg | 40 kg | 55 kg | 66 kg |
*1 PTP control: Each of the specified axes moves to the end coordinate at a set speed. Interpolation control: Each of the specified axes moves to the end coordinate at an interpolated composite speed.
*2 These values vary depending on the operations, the weight and gravity center of the loaded object, or other factors.
*3 This value is measured by the method prescribed by Musashi Engineering (measuring method in conformity with JIS).
*4 When options are not mounted. Varies according to the set speed, set acceleration/deceleration time, and operation mode.
*5 Width and Depth are the dimensions of the lower section of the case.
Key Features:
- High Levels of Dispensing Quality for Enhanced Yield
- High-speed Stable Operations of Heavy-duty Tools and Work Pieces
- Supporting SynchroSpeed™ Function
- Improved Linkage With the Dispenser to Aim for Higher Dispensing Quality
- Reconfigurable Dispense Conditions From Robots
- Simple Test Shot for Improved Dispensing Quality
- 3D/Spline Interpolation
- Nozzle Adjuster
- Number of Input/Output Signal Points: 26 General-purpose Input Points, 26 General-purpose Output Points
- Program Entry Method: Teaching Pendant, PC
- New Teaching Pendant With Improved Usability, Interactive Navigation, Easy to View Large Backlight Screen, Inter Robot Program Copy and Embedded Stopwatch
- Program Capacity: 40,000 Steps (999 Channels)
- Program Storage System: Internal Memory, Back-up on PC With Dispensing Pattern Editing Software
- Program Editing Software: MuCAD V (Optional)
- Enhanced Hardware Configuration
- No Misalignment and No Loss in Synchronization
- Built-in Brake to Prevent Robot Head From Falling During Emergency Stops
- External Input/Output 26 Ports
- High-speed USB Communication
- Other Functions: Test Shot, Eject Condition CH Switching, SynchroSpeed™, Data Transfer With Teaching Pendant
- Other Options: Leakage Protection Box, Teaching Pendant Set, External Operation Box (Horizontal/Vertical), Work Bases, Suction Box for Work Bases, Holder Units, Nozzle Adjuster, Nozzle Cleaner, Protection Cover (Door Type / Optical Axis Type)
- CE Marking Certified, EU RoHS Compliant
Applications: Fully Automated, High-precision, High-rigidity and Fast Dispensing of Optical Adhesives, Solder, UV Adhesives, Threadlockers and Other Fluids
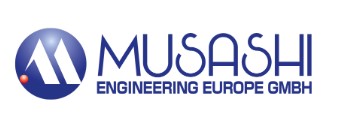