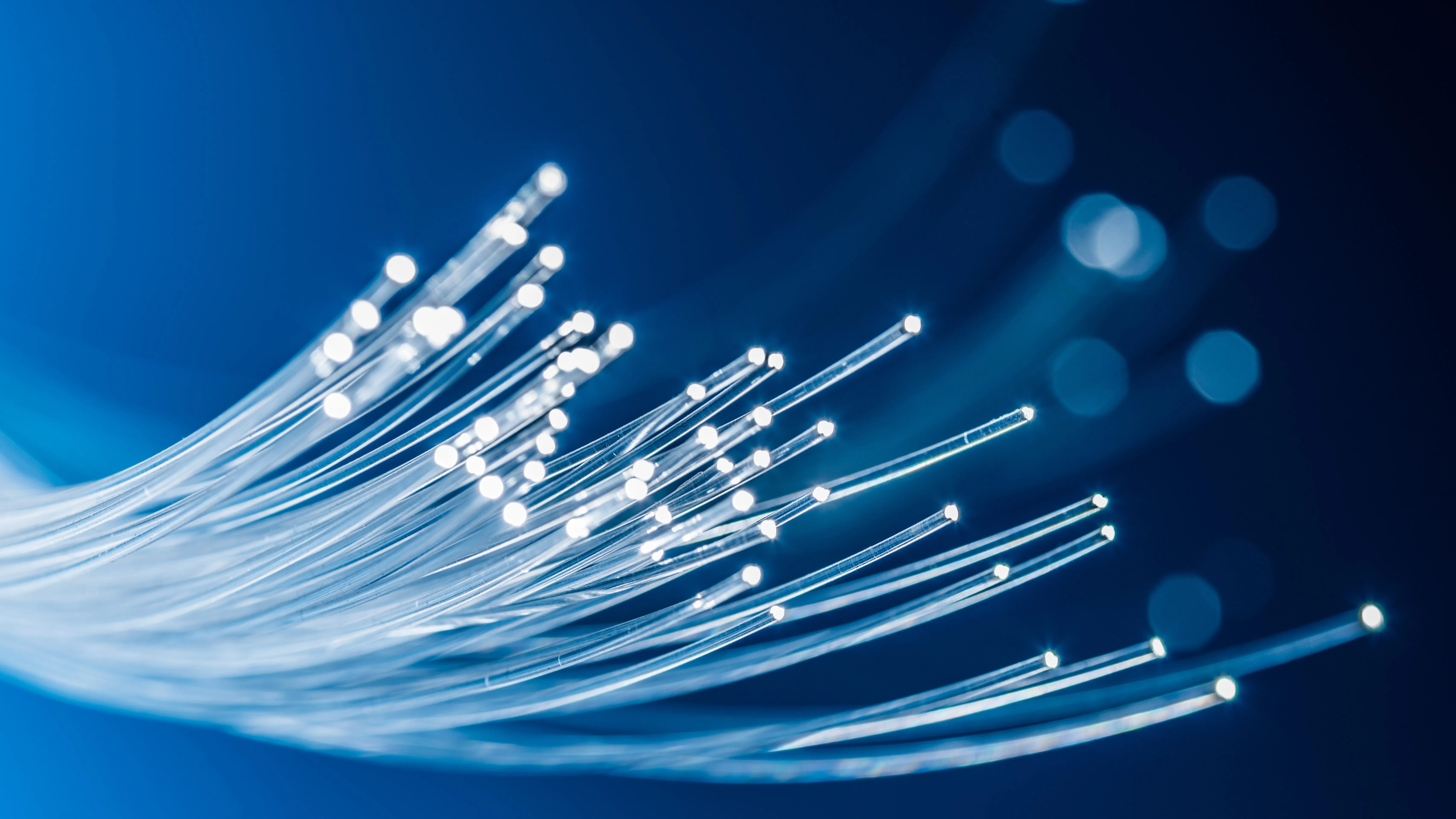
Streamlining Multi-Fiber Processing Step by Step
The demand for high-speed internet and reliable communication networks continues to surge, and so is the need for efficient and precise multi-fiber processing. The process involves multiple intricate steps, each requiring meticulous attention to detail to ensure optimal performance.
Multi-fiber processing presents several challenges that can impact the efficiency and quality of fiber optic networks.
Key Challenges in Multi-Fiber Processing
Precision and Consistency: Ensuring that each fiber in a multi-fiber array is processed with the same level of precision and consistency is critical. Variations can lead to signal loss and degraded performance. Additionally, dust, debris, and other contaminants can compromise the quality of fiber optic connections, leading to signal degradation and increased maintenance costs. Maintaining high standards of quality control throughout the processing stages is essential to prevent these issues.
Demands on Workforce: Skilled workers are increasingly rare, and training new employees to the required level of expertise can be time-consuming and costly. Automation becomes an attractive solution as it helps maintain high standards of quality and precision without relying heavily on a highly skilled workforce. By automating key steps in the processing workflow, companies can ensure consistent results and reduce the risk of human error.
Efficiency and Scalability: As demand for fiber optic networks grows, the ability to scale up production efficiently becomes increasingly important. Ensuring that the processing workflow can be expanded without compromising quality or increasing costs is a significant challenge.
Solutions to Overcome These Challenges
To address these challenges, a suite of advanced tools and technologies can be employed, enhancing both efficiency and quality from start to finish. These products can be used together in a seamless process chain to optimize the entire workflow, or individually to streamline specific steps within the process.
OpTek LCS500: Precision in Stripping and Cleaving
The OpTek LCS500 is a revolutionary machine that simplifies the fiber stripping and cleaving process. While the stripping is performed mechanically and the cleaving is done using laser technology, the key advantage of the LCS500 lies in its ease of operation. This machine is designed to be user-friendly, reducing the likelihood of errors and making it accessible even to less experienced operators. By minimizing the complexity of these tasks, the OpTek LCS500 helps address the skilled labor shortage and ensures consistent quality. The precision of mechanical stripping and laser cleaving ensures that the fiber ends are perfectly prepared for subsequent processes, reducing the likelihood of defects and improving overall reliability. This makes it particularly suitable for applications involving MT-Ferrules and fiber arrays.
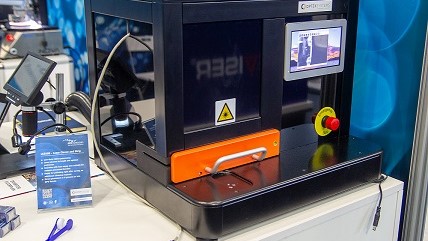
Gator Fiber Cleaners: Versatile and Efficient Cleaning
The Gator Fiber Cleaners from KrellTech are versatile tools designed for prepping stripped ribbon fibers prior to polishing, inserting, and other processes. The Gator cleaners can be used dry or with a cleaning solvent, making them adaptable to various cleaning needs. Their design ensures that fibers are thoroughly cleaned, removing debris and residual buffer coating material. This thorough cleaning process is crucial for achieving high-quality splices and terminations, as any remaining contaminants can lead to signal loss or degradation.
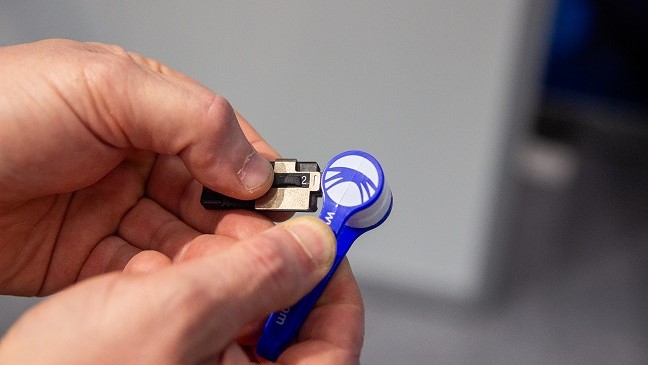
Connected Fibers 1Cure-VI-X and 1Cure-HI-X Epoxy Curing Ovens: Advanced Curing Solutions
For applications requiring epoxy curing, the 1Cure-VI-X and 1Cure-HI-X ovens from Connected Fibers provide advanced solutions. These ovens feature the latest PID microprocessor technology, offering stable and uniform temperature control. The programmable ramp/soak features ensure that the epoxy is cured optimally, enhancing the durability and performance of the fiber optic connections. These ovens are versatile, supporting both vertical and horizontal curing applications, including MT-Ferrules. Moreover, they boast a very easy and straightforward graphical user interface, which simplifies operation significantly. This user-friendly interface not only reduces the learning curve for new operators but also enhances productivity and quality by minimizing operational errors and making the curing process more intuitive and efficient.

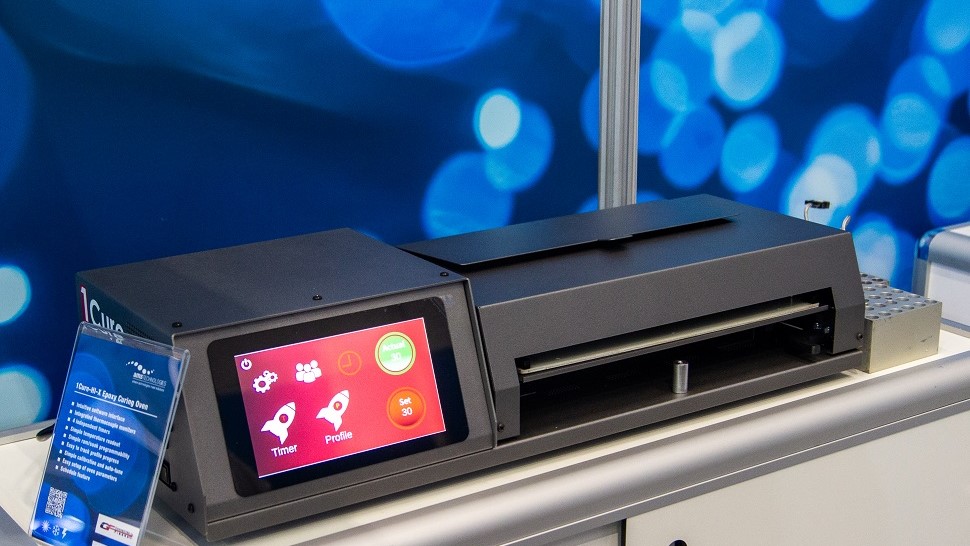
UWave UV Chamber Curing Oven and NTT-AT Optical Adhesives: Efficient Curing for V-Groove Arrays
For curing V-Groove Arrays, the combination of the UV Chamber Curing Oven from UWAVE and high-precision optical adhesives from NTT-AT offers an efficient solution. The UV LED irradiation oven is designed for a wide range of applications, including bonding and curing. Its ergonomic design allows for precise control over the curing process, ensuring consistent and repeatable results. This compact solution contains nearly all the customization options found in larger devices, making it highly versatile. The reflective curing chamber exposes the sample to UV radiation from all sides, leading to even curing and preventing cracking. Additionally, work safety is a top priority, as exposure to UV radiation can pose health risks to operators. The NTT-AT optical adhesives provide sub-micron accuracy in fixation, ensuring that the optical components are securely bonded with minimal positional change during curing. This precision is crucial for maintaining the alignment and performance of the optical network.
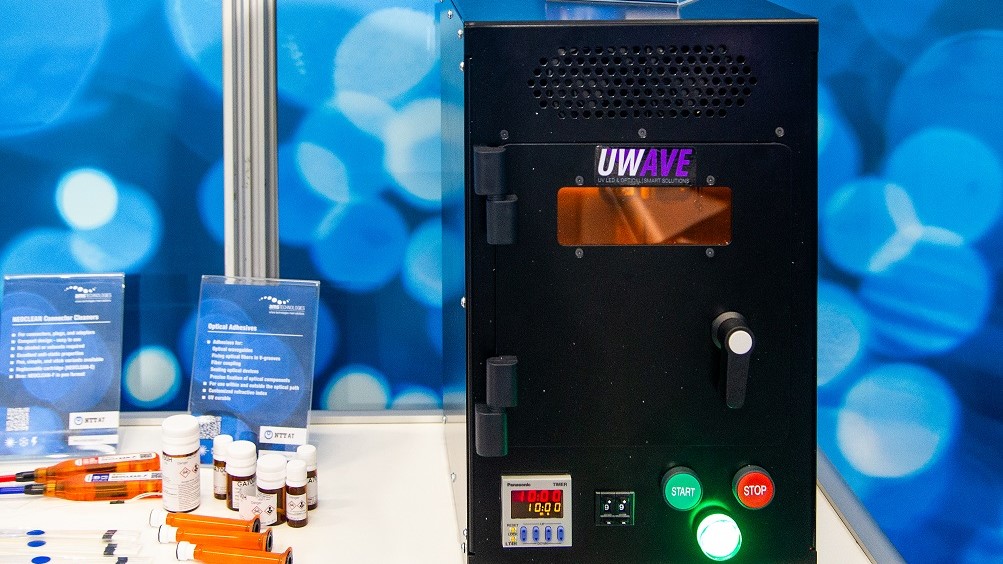
KrellTech NOVA Polisher: Final Touch for Optimal Performance
The final step in the process is polishing the fibers, and the NOVA Polisher from KrellTech is designed for this purpose. The NOVA Polisher offers maximum flexibility for optical surface processing, supporting a variety of polishing applications from bare-ribbon fibers to MT-Ferrules and fiber arrays. Its automated and programmable features make it suitable for both R&D projects and high-volume production, ensuring that the fibers are polished to perfection. Unlike conventional polishing machines, the NOVA Polisher allows for the customization of the base with many different fixtures, accommodating a wide range of applications. This flexibility ensures that each fiber is finished to the highest standards, providing low insertion loss and high return loss.
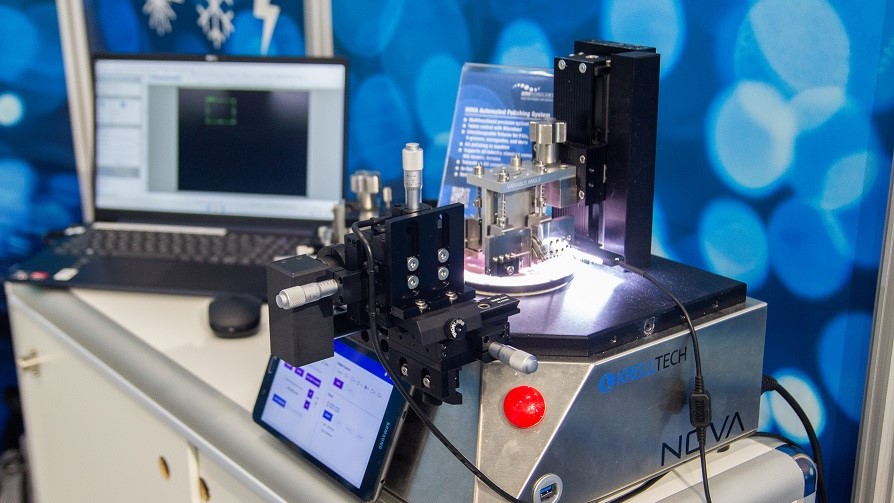
Conclusion
By integrating these advanced tools and technologies, the process of multi-fiber processing becomes more efficient and reliable. From the initial stripping and cleaving to the final polishing, each step is optimized to ensure the highest quality and performance of the optical network. This comprehensive solution not only enhances productivity but also ensures that the end product meets the stringent demands of modern fiber optic communications.