Aspheric lenses: when the sphere is not enough
In the beginning was the sphere
Since the first lenses were used systematically as reading aids (from about the 13th century), at least one of the two optically effective surfaces of a lens was part of a spherical surface (sphere), i.e. curved with a constant radius over the entire surface. Not least because of this singular dimension, a manufacturer does not need too much know-how and effort to produce such spherical lenses by grinding a glass body – one of the main reasons why spherical lenses formed the norm for centuries and were synonymous with an optical lens.
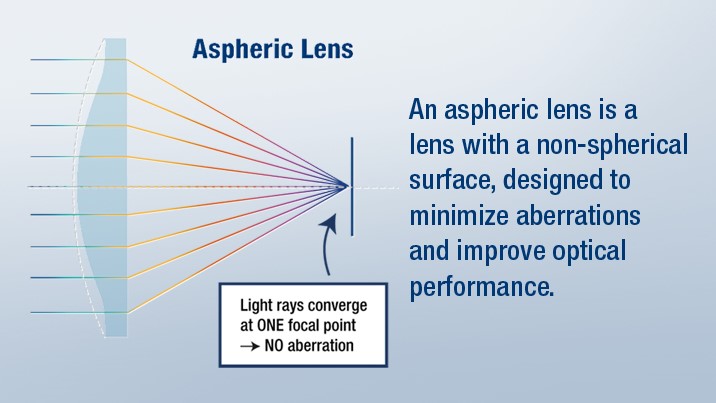
Why not just always use aspheric lenses?
If aspheric lenses are so much better, why not just use them all the time? The short answer: because the surface is much more complex than that of a spherical lens. While a single radius of curvature is sufficient for the mathematical definition of a spherical lens, a rotationally symmetrical aspheric lens is usually defined by a conic section (circle, ellipse, hyperbola, but usually a parabola with a radius of curvature and a conic constant in the parabolic term) plus a correction polynomial with several coefficients for higher-order deformations. Such a complex surface is, of course, much more difficult to produce in high, consistent quality than the simple spherical variant, and with disproportionately greater effort. For a long time, since the early 17th century to be precise, aspheric lenses have been considered the optimal solution for light refraction – but at the same time far too expensive to manufacture, which is why they were only used very sporadically.
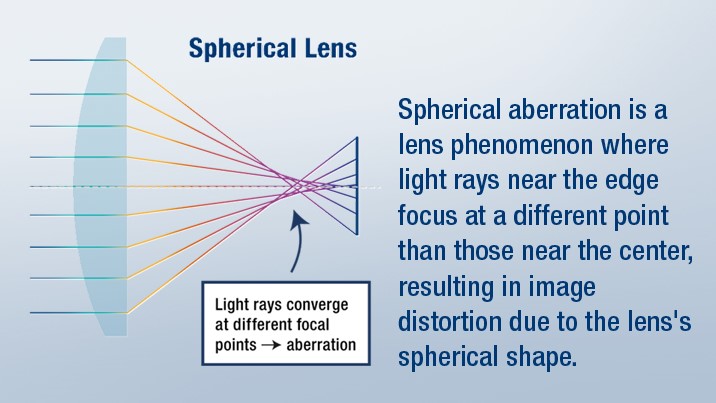
What are molded aspheric lenses?
Traditionally, aspheric lenses are individually grinded and polished from glass preforms in complex processes, for example computer-controlled (CNC polishing), with magneto-rheological finishing or using diamond turning technology. In contrast, precision glass molding is a much less complex manufacturing process for aspheric lenses. In precision glass molding, optical glass blanks are heated to such an extent that the surface becomes soft enough to be pressed into an aspheric mold.
It all depends on the mold
To ensure that the lenses produced at the end of the manufacturing process fulfil the required detailed dimensions exactly and reproducibly, this mold must, however, meet high requirements. A lot of effort and a high amount of initial costs are necessary to ensure that the inside of the mold has an extremely smooth surface without even the tiniest indentations or bumps – and with a high degree of durability so that this surface can withstand many pressing processes without any loss of quality. In addition, when calculating and manufacturing the mold geometry, manufacturers must consider that it precisely compensates for material shrinkage when the finished pressed lens cools down.
Extreme pressure on the aspheric lens – and on its price
But once these challenges are overcome and the mold is finished and in place, suppliers can produce aspheric lenses at a much lower cost than those of conventional manufacturing techniques. Because our experienced manufacturing partner uses very advanced glass molding technology, aspheric lenses are produced with consistently high quality in large quantities at an affordable price. Aspheric lenses offer further savings in applications where a single aspheric lens can replace an entire set of multiple spherical lenses – rendering the overall optical system less complex, more compact and lighter, while often even increasing its optical performance.
Click here for an overview of our portfolio of precision molded aspheric lenses: standard, infrared and mounted in stainless steel holders:
Contact us if you would like to talk with one of our sales managers to find the most suitable lens for your application. Send us your request via the contact form, we will get back to you quickly!